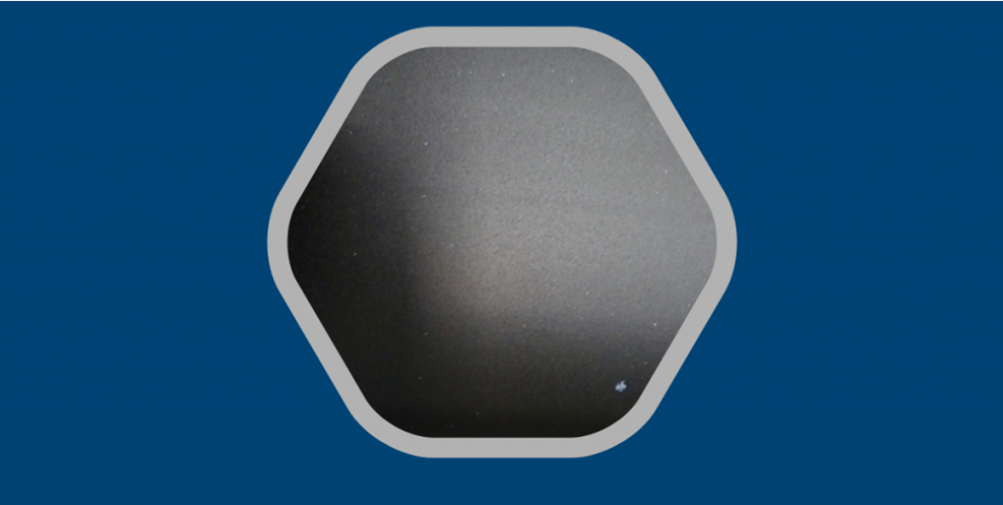
Quando sui pezzi anodizzati e colorati elettroliticamente compaiono piccoli puntini bianchi non rimovibili, tali manufatti risultano invendibili e richiedono perciò ulteriori lavorazioni. Per questo, è molto importante localizzare rapidamente ed eliminare la causa del problema.
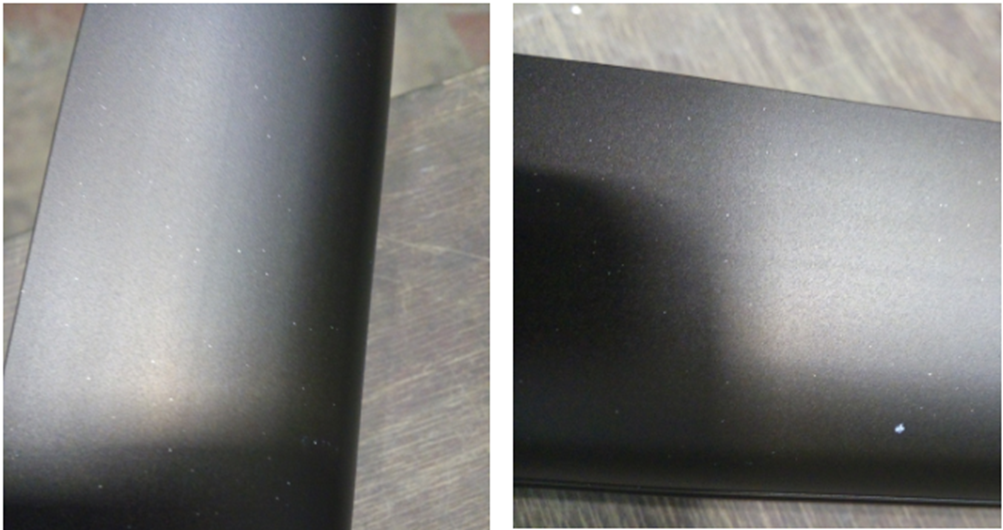
La foto sopra mostra un profilo difettoso in cui sono comparsi i puntini bianchi. Infatti, durante un’operazione di anodizzazione con colorazione elettrolitica, sono apparse tali imperfezioni sulla superficie anodizzata di colore bronzo, che sembravano buchi di spillo. Il difetto è immediatamente visibile su superfici scure, ma non sul prodotto anodizzato naturale.
La prima indagine sulle cause del difetto
Per capire quale fosse la causa dei difetti, è stata esaminata più attentamente l’area intorno al bagno di colorazione elettrolitica. È emerso rapidamente che la fonte del problema non aveva a che fare con la materia prima, le impostazioni del bagno di colorazione, il trattamento meccanico preliminare, la sequenza di processo prima della colorazione, i parametri elettrici, il contatto durante l’anodizzazione o la colorazione.
Tuttavia, l’analisi per la contaminazione dei bagni di processo ha rivelato un contenuto aumentato di cloruri nei bagni di anodizzazione e nella neutralizzazione. Quindi, credendo che la causa del difetto fosse stata identificata, i bagni sono stati rinnovati e i pezzi hanno subito una nuova colorazione. Tuttavia, nonostante l’assenza di contaminazione da cloruri, i puntini bianchi sono riapparsi.
Ulteriori analisi per arrivare alla fonte reale del problema
Durante ulteriori indagini, anche le zone che circondavano l’impianto di anodizzazione sono state ispezionate più da vicino. Qui hanno attirato l’attenzione i ventilatori montati sul muro dell’edificio sul lato dell’impianto, che avrebbero dovuto aspirare i gas prodotti dall’area di produzione. Per estrarre l’aria di scarico sono stati utilizzati in totale 5 ventilatori.
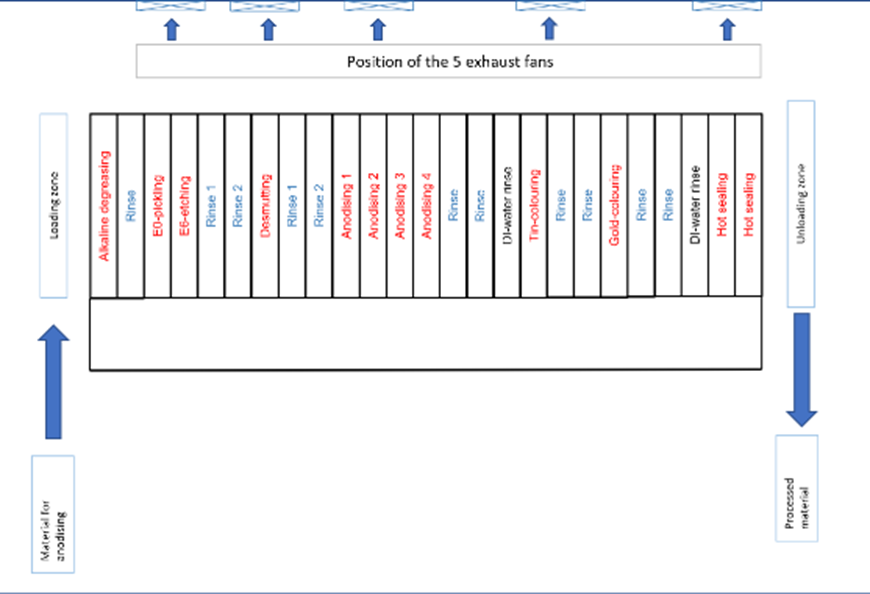
Impianto di anodizzazione con i 5 aspiratori
Il flusso d’aria del sistema è approssimativamente mostrato nello schema seguente. È evidente qui che i fumi provenienti dalle vasche E0 ed E6 raggiungono anche la parte posteriore del sistema. Per i pezzi che si trovano in questa area, c’è quindi il rischio che piccole particelle del processo di attacco alcalino vi si depositino sopra. Il pericolo è maggiore quanto più attacco alcalino viene effettuato e quanti più fumi vengono prodotti. Nell’impianto, è stato osservato che le particelle si depositavano sul materiale particolarmente nell’area dei bagni di colorazione. L’esame microscopico del materiale difettoso ha mostrato che nell’area delle macchie solo il colore era stato rimosso, ma non era avvenuto alcun attacco corrosivo visibile (formazione di buchi) sulla superficie. Quindi, sebbene l’alcalinità delle particelle comportasse una decolorazione selettiva sulla superficie, non era sufficiente per avere un effetto corrosivo della superficie ossidata.
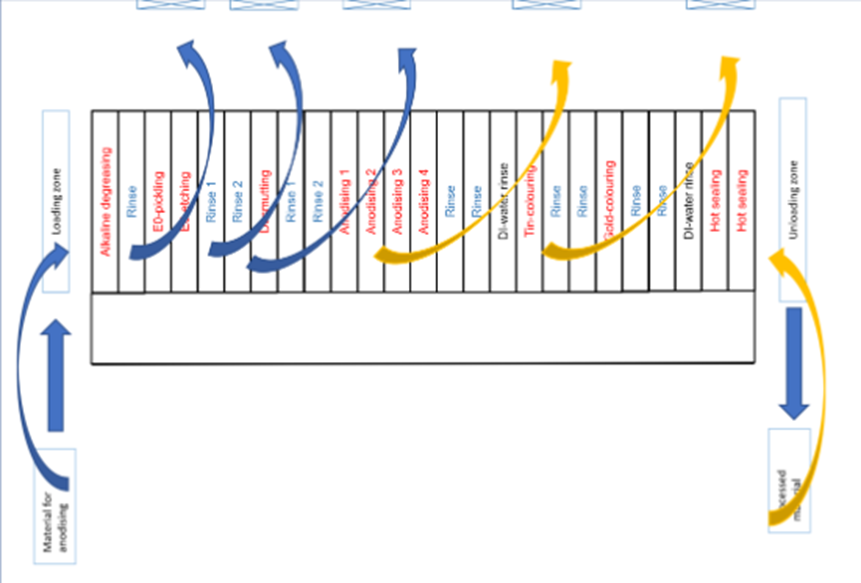
Convogliamento dell’aria esausta nell’impianto
La soluzione: modifica del percorso dell’aria di scarico nell’ambiente
Una semplice misura correttiva nel percorso dell’aria di scarico ha risolto il problema. A tal fine, i due ventilatori posteriori (vedi flusso d’aria delle frecce arancioni) sono stati spenti nell’area del bagno di colorazione e della sigillatura a caldo. A causa dell’assenza di aspirazione delle particelle corrosive in questa area, è stato possibile evitare efficacemente la contaminazione della superficie colorata. I manufatti successivamente prodotti erano nuovamente privi di difetti e il problema è stato risolto. Nonostante ciò, anche se questa soluzione al problema era semplice ed efficace, non è l’ideale. È infatti meglio rimuovere i fumi direttamente al punto di origine, ad esempio mediante una adeguata estrazione locale presso il bagno o tramite un’adeguata chiusura ed estrazione del supporto per i pezzi.